
Sustainable manufacturing – why local kinetic energy storage has a growing part to play on the journey to net zero
Kinetic energy storage at MW plus scale is a proven, suitable sustainable solution for a multitude of manufacturing applications
The immediate and long-term power challenges faced by UK manufacturing range from coping with power price surges to creating a sustainable path to net zero by 2050. The manufacturing and process sectors are among the UK’s largest energy consumers.
Figures* show that UK manufacturing accounted for 16% of UK greenhouse gas emissions in 2019. Energy consumption levels include manufacturing and industrial services –more than 42GWh; chemical manufacturing – 40GWh; food, drink, and tobacco manufacturing 34GWh and iron, steel, and metal manufacturing –17GWh.
In every manufacturing sector companies face short-term objectives to find cheaper and cleaner power while building a long-term strategy for reaching net zero by 2050. While maintaining clean, stable power to the production lines remains the priority for manufacturers, they must also find innovative power solutions that don’t add to their GHG profile.The challenge of creating a sustainable UK manufacturing base means seeking all possible GHG emission reductions at every point in the operation. This means exploring every opportunity to measure, remove and reduce embodied and operational carbon from all power related activities.Eradicating GHGs starts with life cycle analysis of power plant and machinery of every unit and component used to power production lines and ancillary services. Increasingly manufacturers must be seen to adopt a whole of life perspective on environmental impact and TCO. This will require detailed analyses of complex supply chains and production processes. It will extend to evaluating raw material extraction and processing, supply chains, manufacturing processes, production environments, delivery, lifetime operation, decommissioning, disposal, re-use and recycling options.
In terms of power protection and back up, overcoming so many challenges requires new thinking about energy storage at a local level. A good starting point is a comparison between solutions based on chemical batteries and clean mechanical kinetic technologies. Such comparisons should evaluate the sustainability and performance credentials through a full life cycle analysis (LCA) which will include embodied carbon cost, operational carbon emissions, maintenance and ultimately, recycling.
Flywheel Energy Storage for Manufacturing Applications
Different manufacturing applications have particular power protection challenges. But whether it is robots assembling cars, pharmaceutical manufacturers maintaining sterile environments or food producers ensuring freshness and safety, all processes are becoming increasingly automated. Any sudden loss of power can have devastating effects.
This means the supply of constant, clean, conditioned power that is located close to the production environment is growing. In such environments even the shortest breaks in power supply or perturbations are unacceptable.
Piller’s POWERBRIDGE™ flywheel kinetic technology has many features which makes it ideal for manufacturing. POWERBRIDGE™ units are often deployed in manufacturing environments where a key requirement is the ability to power down safely. Automatically activated Flywheel technology providing instantaneous power means a facility can power down in a safe and gradual procedure. Stored energy does not require recharging from an external source so when any outage occurs the Flywheel assumes the power load immediately.
A Flywheel energy store is the ideal solution for applications that don’t require minutes of autonomy.
Features such as the wide operating temperature range, small footprint and low maintenance requirements mean Flywheels can be deployed close to or directly into factory floor production environments.
Features and capacity
For manufacturers the use of kinetic flywheels instead of batteries is increasingly being recognised as a proven and effective method of providing efficient power back up.
Flywheels remove the need for tightly controlled heat and humidity environmental conditions, replacement, and long recharge times associated with large battery installations.
The POWERBRIDGE™ PB60+ is a highly compact, efficient, and practical replacement for conventional batteries. The unit can deliver power above 3MW and provide 1MW of electrical power for over 60 seconds.
In capacity terms Piller POWERBRIDGE™ PB60+ flywheels provide 60 Mega joules – part of the broadening range of capacities offered by proven POWERBRIDGE™ flywheel products.
With the PB60+, the Piller PB kinetic energy storage systems range extends from 3.6MJ to 60MJ+.
The highly reliable, easily maintainable POWERBRIDGE™ is an environmentally clean source of back-up power. These flywheels offer a service life of typically 25 years, resulting in minimal disruption in operation associated with battery refresh cycles, and low whole life costs.
Flywheels are electrically coupled to the UPS and can be deployed irrespective of the type of load to be supported offering unrivalled service life and reliability thanks to uncomplicated architecture and low component count.
Lower costs, lower carbon, higher efficiency
A kinetic flywheel can reduce operational and capital expenditure delivering a TCO 40% lower than battery solutions.
There is much discussion about cradle to grave environmental impact of Flywheels versus batteries and the carbon costs at every stage including installation, initiation, and operations and whether in embodied carbon terms Flywheels are more sustainable when compared with VRLA and Lithium-ion batteries.
What is not in doubt is that the flywheel supports production environment infrastructure with 98% power quality protection with high efficiency permanent energy storage.
Mechanical Flywheel kinetic energy provides instantaneous back up of infrastructure without batteries containing toxic chemicals.
The constant spinning of the compact rotor maintains an energy source for instant activation as stored kinetic energy converts to electricity which supports the load.
If a sudden grid perturbation occurs a facility’s power is shielded by kinetic energy stored in the flywheel.
Conclusion
Any full life cycle analyses of energy storage metrics that encompass TCO, total environmental impact, high efficiency operation with low maintenance and few shutdowns, delivering high power density is a complex undertaking.
Flywheels made using environmentally inert materials that are easily recycled and reused, such as Piller’s POWERBRIDGE™ range are being used as an efficient and sustainable local energy storage solution for manufacturing environments across the world.
Piller believes that Flywheel energy storage has a growing role as an energy storage solution for manufacturers.
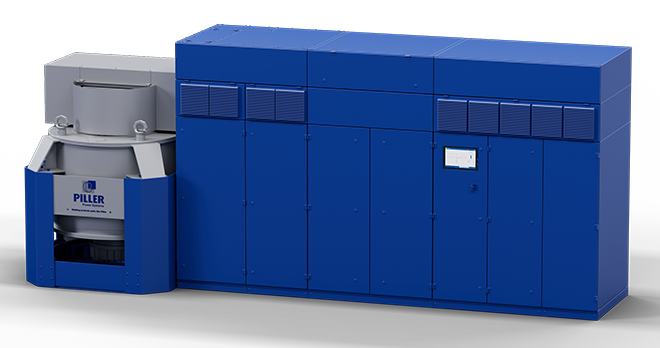
Piller UNIBLOCK™ UPS with POWERBRIDGE™